Are you curious about the latest in augmented reality (AR) and virtual reality (VR) tech? You’ll be amazed by how a new manufacturing process is changing the game for AR/VR devices. THY Precision’s Injection Molding Optical Lenses process is making thinner, lighter optical lenses. These lenses are key for the next level of AR/VR tech.
Before, AR/VR lenses were made with refractive optics, which have curved surfaces. But now, Injection Molding Optical Lenses lets us make “flat optics” or “meta optics.” These use diffractive nanostructures for better lens performance. This change is huge for making AR/VR devices smaller, lighter, and more efficient.
Key Takeaways
- The Injection Molding Optical Lenses process step by step is changing how we make AR/VR lenses.
- Flat optics or meta optics bring big size, weight, and power (SWAP) benefits over old refractive optics.
- THY Precision leads this change, using Injection Molding Optical Lenses for precise, high-performance lenses.
- This process lets us make diffractive nanostructures for new lens designs that are thinner and lighter.
- This leap in precision optics is a big deal for AR/VR, making devices more compact and immersive.
Understanding the Injection Molding Optical Lenses Process Step by Step
The injection moulding process is a precise way to make complex parts, like those in AR and VR devices. It starts with melting thermoplastic resin pellets. Then, this molten plastic is pushed into a mold under high pressure to form the desired shape.
Resin Pellets and Melt Delivery System
First, thermoplastic resin pellets are added to a heated barrel. These pellets become a liquid state, called the “melt.” This liquid is then pushed through a nozzle into the mold, taking the shape needed for optical parts.
The melt delivery system is key for a smooth flow of plastic into the mold. It includes the screw, barrel, and nozzle. Heat, pressure, and the mold’s design make it possible to create complex optical parts for AR/VR technology.
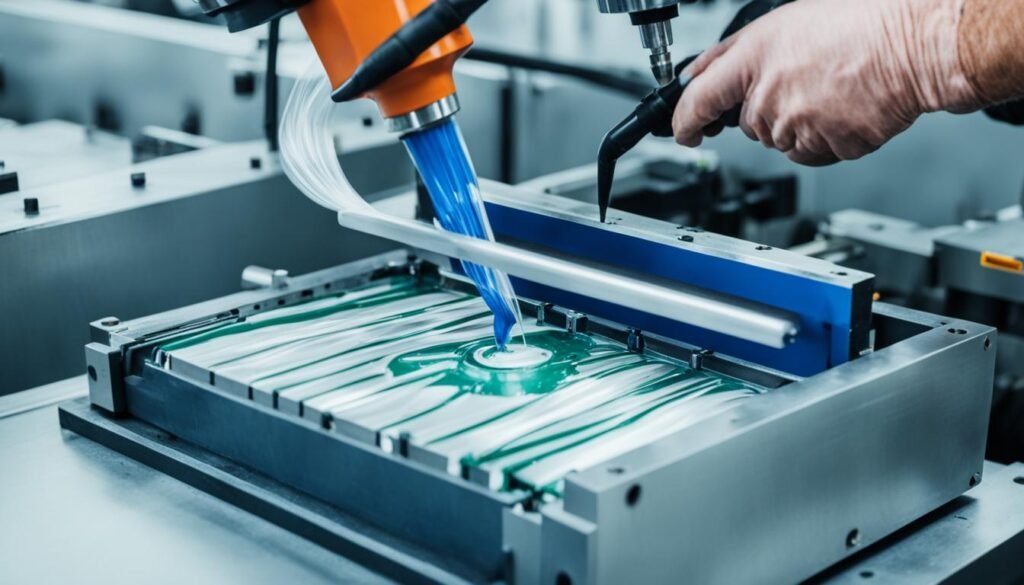
“The injection moulding process is a true game-changer in the world of optical component manufacturing, allowing for the creation of complex, high-precision lenses and other critical elements that are essential for the next generation of AR and VR devices.”
Injection Molding Optical Lenses – Mold Cavity Filling: Precision and Control
The injection moulding process step by step is key for making optical lenses. The mold cavity filling stage is very important. At THY Precision, we know how crucial precision and control are in plastic Injection Molding Optical Lenses for optics.
When making lenses, the molten material must go into the mold cavity with precision. THY Precision uses top-notch injection moulding process step by step methods. These methods control the molten material’s flow, reducing any mistakes or changes in the lens shape. This precision is vital for making the nanostructured surfaces needed for flat and meta optics. These surfaces must have the right shape and position to work well.
To get this precision and control right during mold cavity filling, THY Precision uses special techniques and tech. These include:
- Precise control of the melt temperature and injection speed for even material flow
- Advanced flow simulation and modeling to improve mold design and fill pattern
- Real-time monitoring and adjusting of the injection process to keep part quality consistent
With these injection moulding process step by step skills, THY Precision can make the high-quality optical lenses needed for AR/VR tech.
“At THY Precision, we aim to expand the limits of plastic injection molding for optics. Our focus on precision and control in mold cavity filling drives our success.”
Injection Molding Optical Lenses – Cooling and Part Ejection: Critical Stages
After filling the mold, the next steps are cooling and ejecting the part. The mold cools down, letting the plastic harden into the right shape. This cooling is done carefully to keep the plastic’s properties and quality for AR/VR parts.
The Cooling Cycle
The cooling part of the process is key for making good optical lenses. The mold’s temperature and cooling speed must be just right. This helps the plastic cool slowly but surely, avoiding defects that could ruin the lens.
A good cooling cycle is vital for getting parts out easily and keeping the plastic parts strong.
Cooling Stage | Importance |
---|---|
Mold Cooling | Allows plastic to solidify and take lens shape |
Cooling Rate Control | Prevents warping, stress, and other defects |
Optimal Cooling Time | Ensures complete solidification before ejection |
Once the plastic is cool, it’s ejected from the mold, ending the molding cycle. These steps are key for making top-notch AR/VR parts.
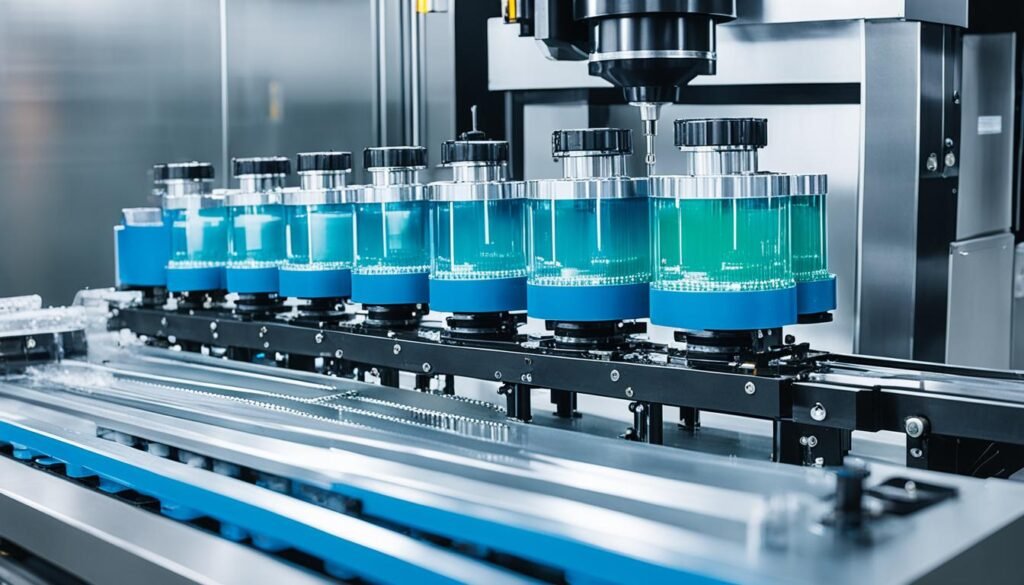
Injection Molding Optical Lenses Machines: Enablers of Precision Optics
The injection molding machines at THY Precision are vital for making flat optics and meta optics. These machines control the temperature, pressure, and flow of plastic perfectly during the injection moulding process step by step. This lets THY Precision make lenses with the detailed nanostructures needed for AR/VR tech.
These injection molding machines are reliable and can make more parts as needed. This meets the high demand for small but powerful optical parts in the fast-growing AR/VR market. By always using the newest plastic injection molding tech, THY Precision keeps making parts that are both precise and high-quality for the next AR/VR generation.
Feature | Benefit |
---|---|
Precise Temperature Control | Ensures consistent melt viscosity for accurate part replication |
Advanced Pressure Regulation | Enables filling of intricate mold cavities without defects |
Optimized Melt Flow | Supports the production of flat optics and meta optics with complex surface features |
THY Precision’s use of top-notch injection molding machines shows their dedication to quality precision optics for AR/VR. By always innovating and updating their gear, they stay ahead in this fast-changing market.
“The precision and control offered by our injection molding machines are crucial to the production of the advanced optical components that power the latest AR/VR technologies.”
Conclusion
The injection molding process has changed the game for making AR/VR lenses. Companies like THY Precision are at the forefront. They use this method to make “flat optics” or “meta optics” with tiny nanostructures. These lenses are smaller, lighter, and use less power than old ones, making AR/VR tech better.
THY Precision controls every step of the injection molding process. From melting resin to cooling, they make sure each lens is perfect. This skill lets them make “nano-optics” and “diffractive optics” that change the AR/VR world.
As AR/VR tech gets more advanced, the injection molding process will be key. THY Precision is leading with their innovative lens making. They’re making AR/VR experiences better and more accessible for everyone.